Safety
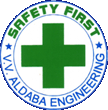
SAFETY POLICY STATEMENT
V.V. Aldaba Engineering shall promote SAFETY
with QUALITY SERVICE. With our Safety Programs, we
shall adhere to the Client's Safety policies in preserving
Life, Health, Environment, Facilities, and Resources.
VVAE shall implement work at the job site with the aim
of ZERO LOST TIME INJURY.
We, therefore, enjoin all our involvement in strict
Observance and enforcement of Safety without affecting
Performance and cost.
1. OBJECTIVE
To achieve Zero Lost Time Accident for the duration of the projects.
To promote and protect the Health of all personnel engaged with the projects.
To preserve and protect the environment.
2. LEADERSHIP AND ADMINISTRATION
This involves the issuing of procedures, safety rules and awareness programs to ensure the safety and health of all employees.
All work that will be carried out by the Engineer is subject to VVAE's Health, Safety and Environment standards or of the customers whichever is stringent. In terms of these standards, it is the responsibility of management to take all reasonable measures to ensure that every person in his employ or on premises observe the requirements of' the regulations.
3. TRAINING
Before anyone can and be allowed to commence work on site they are required to attend an HSE Induction. The Safety Officer carries this out.
- Brief Outline of the Project
- Customer / VVAE Safety Policy
- Safety hazards and awareness
- Work permit system
- Details of First Aid Facilities and Emergency Procedures
- Traffic Regulation
- Personal Protective Equipment (PPE)
- Safe Work Procedure
- Scaffoldings Standards and requirements
- Serious Safety Violations
- Accident / Incident Reporting
- Safety Responsibility
- Discussion on Previous Accidents/Incidents
- Disciplinary Actions
- Safety Incentives and Promotions
4. SAFETY INSPECTION
4.1 WHAT TO LOOK FOR DURING INSPECTIONS
- Guarding and protection devices
- Structural defects and hazardous conditions.
- Functional defects
- Work environment
- Material storage and Personnel exposure
- Practice and procedures
4.2 GUARDING AND PROTECTION DEVICES
- Missing or inadequate guards against being struck by.
- Missing or inadequate guards against striking against.
- Missing or inadequate guards against being caught on, in, or between.
- Missing or inadequate guards against filing from or onto.
- Lack of, or faulty, support, bracing or shoring.
- Missing or faulty warning or signal device.
- Missing or faulty automatic control device.
- Missing or faulty safety device.
4.3 STRUCTURAL DEFECTS AND HAZARDOUS CONDITIONS
- Sharp edges, jagged, splintery, etc., conditions.
- Worn, frayed, cracked, broken, etc., conditions.
- Slippery conditions (for gripping or walking).
- Dull, irregular, mutilated, etc., conditions.
- Uneven, rough, pocked, or with holes.
- Decomposed or contaminated conditions.
- Flammable or explosive characteristics.
- Poisonous characteristics (by swallowing, breathing, or contacting).
- Corroded or eroded conditions.
4.4 FUNCTIONAL DEFECTS
- Susceptibility to breakage, collapse, etc.
- Susceptibility to tripping, falling, etc.
- Susceptibility to rolling, sliding, slipping, etc.
- Leakage of gases, fumes or fluids.
- Excessive heat, noise, vibrations, fumes, sparking, etc.
- Failure to operate.
- Erratic, unpredictable performance.
- Lack of adequate electrical grounding.
- Operation that is too fast or too slow
- Low voltage leaks
- Signs of excessively high or low pressure.
- Throwing off of parts, particles, materials, etc.
- Indication of need for special attention.
4.5 WORK ENVIRONMENT
- Noxious fumes or gases.
- Flammable or explosive fumes or gases.
- Insufficient illumination.
- Excessive glare from light source.
- Hazardous dusts or atmospheric particles.
- Hazardous or uncomfortable temperature conditions.
- Excessive noise.
4.6 MATERIAL STORAGE AND PERSONNEL EXPOSURE
- Unsafe storage that permits easy by persons with equipment.
- Unsafe exposure to heat, moisture, vibration, flame, sparks, chemical action, electric current, etc.
- Congestion of traffic or working space.
- Unsafe attachment of object to agent.
- Unsafe placement of objects in agent.
- Unsafe distribution of objects around agent.
- Protruding objects.
- Use of unsafe storage container.
- Faulty ventilation of stored materials.
- Unsafe traffic layout.
- Poor housekeeping.
- Improperly secured against sudden movement such as falling, slipping, rolling, tripping, sliding, etc.
4.7 PRACTICE AND PROCEDURE
- Correct use of plant, tools and equipment.
- Safety rules and safe operating procedures being followed.
- Correct use and maintenance of personal protective equipment.
- Relevant information available on hazardous materials.
- Employees aware of the need to report hazards.
- All workplace hazards clearly defined in written procedures.
- Employees provided with proper training for the job.
5. HAZARDS ANALYSIS
5.1 Objective
- To identify workplace hazards and make a plan of action to correct them.
- To select an appropriate JIM Team.
- To break a job down into basic job steps.
- To Identify the existing and potential hazards associated with each job steps.
- To develop recommendations to eliminate or control existing and potential hazards.
Four Subsystems within the total workplace System
- People
- Equipment
- Materials
- Environment
These are the questions that should be analyzed
People:
- What contacts are present that could cause injury illness stress or strain?
- Could the worker be caught in, on, or between? Struck by? Fall from? Fall into?
- What practices are likely to downgrade safety?
Equipment:
- What hazards are presented by the tools, machines, vehicles or other equipment?
- What equipment emergencies are most likely to occur?
- How might the equipment cause loss of safety?
Materials:
- What harmful exposures do chemicals present when they are handled?
- What are the specific problems involved in materials handling?
- How might materials cause loss of safety?
Environment:
- Are there potential housekeeping problems?
- What are the potential problems of sound, heat lighting, cold, radiation, or ventilation?
- How might environmental factors cause loss of safety?
6. WORK PERMITSYSTEM
It is an official written record of conditions, requirements, and authorization for specific construction, inspection, maintenance, repair and/or activities to be undertaken in areas designated as restricted.
It is intended to be applied to those activities which represented hazard to company operations, personnel or equipment.
The following general conditions are requirements that should be followed in the issuance of work permits:
- A Work Permit should be obtained by the person doing the work before any mechanical maintenance or repair or construction work is done inside the plant.
- Such permission maybe granted for a specific reason, for a specific activity, for a specific area and for a specific time.
- Before granting the permit, the issuer, the Receiver, and the Leadman (If any) assigned in the area, shall conduct a joint inspection of the site, discuss the aspects of the job, identify potential hazard, and do the following work basic safety checks.
- After listing down and agreeing with the safety precautions and requirements, the issuer shall obtain the signatures of the receiver, the leadman, and the the Gas Tester (if gas test is required) and shall give his approval and go ahead for the work to start.
- The approved work permit shall be posted in the vicinity of the job at all times.
- Upon completion of the work, the permit shall be closed by the signatures of the receiver (and leadman) and verified by the issuer,
7. SAFETY REPORTS AND RECORDS
Successful accident prevention program is based on the knowledge of how and why accident happens. When accident / incident occur, they must be fully investigated to determine the cause and take necessary action to prevent recurrence.
7.1 PROCEDURE TO BE FOLLOWED
- When accident or incident occurs, it must be immediately reported to VVAE Manager or Safety Officer.
- When injury and/ or damage occur the area must be roped-off; until investigation has been completed. Equipment / materials must not be moved, unless causing a serious obstruction, or blocking emergency access routes.
- Minor incident and near miss must be reported to VVAE Safety Officer.
- All injuries shall be reported to Customer clinic for treatment/medication.
- In all cases a report together with Witness statement and sketches must be submitted to Safety Office (Within 24 hrs,) followed by an investigation report (Within 48 hrs.)
7.2 DEFINITION OF ACCIDENT CATEGORY
- LTA (Lost Time Accident) 1 lost working day or more.
- RWC (Restricted Work Case) no lost time but the injured person is assigned to less strenuous job.
- MINOR no lost time, injured person return to his normal job,
7.3 RECORDS
All records must be on the file of VVAE Safety Officer.
8. ENVIRONMENTAL PROTECTION
Engineer's site management shall take appropriate measures in consideration of site conditions and surroundings.
8.1 SOLID WASTE
In plant construction, the following solid waste will be produced and appropriate disposal methods shall be considered.
- Steel scrap material such as pieces of steel pipes, structure materials, etc.
- Concrete and asphalt material
- Excess excavated soil
- Combustible material such as timber and veneers for forming work
- Solid toxic chemicals
All waste generated in the facility will be disposed on the Customers designated waste disposal area. Customers waste disposal procedure will be followed. Hazardous waste material (i.e. asbestos) will only be removed by customer approved hazardous waste contractor. It is prohibited to dump any solid waste in public or non-designated areas.
It is important that solid waste material shall be segregated according to nature of material and method of disposal. Mixture of all solid material will cause the difficulties of disposal and hamper the smooth operation.
Recyclable steel material for disposal shall be handed over to enterprises which can change these materials into usable form if such enterprises are available in the country of construction site.
Material which do not cause any contamination to the surrounding soil through the process of penetration shall be buried in an excavated pit. Such pits will be approved and designated by customer or local authority. If necessary, pit shall be barricade with a protective concrete wall.
If material are combustible and do not produce an adverse influence on air pollution, they shall be burnt in a furnace. If materials are combustible but produce harmful emission of gases when burnt, it is prohibited to do so.
The disposal of solid chemicals shall be determined carefully by examining the nature and characteristics of the chemical.
Solid toxic Chemicals shall never be disposed of in any place. Method of disposing this material shall be studied and determine at the beginning stage of the project, if the production of such chemical is expected.
8.2 WATER POLLUTION
VVAE should provide water container on site and coordinate with Customer proponent for possible source of portable at site for workers consumption. Worker must not take or drink water at site without Customer approval.
8.3 SPILLED OIL AND GREASE
Maintenance shop for construction equipment will be a source of oil and grease spillage and used motor oil.
Motor oil for disposal and oil spillage shall be collected temporarily into an appropriate container. These shall not be disposed of in any public sewer system.
If a system of recovering such oil and / or oil contaminated water treatment is available, these shall be sent on such facility.
If such system is not available, oil and skimmed oil shall be burnt using a proper furnace or burning facility.
8.4 AIR POLLUTION
VVAE Construction management and supervisors shall check type and year of manufacture of construction equipment during the construction planning. If these are very old and seem to have deteriorated engines, they shall instruct the maintenance to take appropriate measures such as overhauling exigines and improving the frequency of maintenance service.
9. SAFE WORK PRACTICE
9.1 MATERIAL HANDLING
Material handling forms a large part of construction work, There are many areas in which difficult, costly and frequently dangerous manual work handling could be replaced with machines. This section outlines minimum safety precautions to be observed by employees who will work with material handling equipment:
- Operators of material handling equipment must be trained, tested and authorized by proper authorities.
- Material handling equipment must
be:
- Maintained in good working condition.
- Properly used with due respect to Safety.
- Construction sites on which equipment
are used:
- Must be safe and must have suitable access ways.
- Traffic must be organized and controlled as to secure their operations.
- Special safety precautions must be taken for equipment when maneuvering in backwards.
- Assistance of an experienced signalman shall be available when the operator's view is restricted,
- Adequate precautions shall be taken to prevent accident when equipment is being operated in dangerous proximity to live electric wire.
- Preventive measures shall be taken to avoid the fall of equipment into excavation or water.
- Equipment shall not travel on bridges and embankments unless it has been found safe to do so.
- Where appropriate equipment shall be fitted with protection to protect operator from falling materials.
- Equipment shall not be left on a slope with engine running.
- All shafting gears, chains, belts, cranks, and any revolving parts of the equipment must be closely guarded.
- Before making any repair, adjustment or replacement of parts, the equipment must be stopped or deactivated so that it cannot be unintentionally started.
- The engine must be stopped before re-fuelling takes place.
- Passengers shall not be permitted on cranes, dozers, loaders, backhoes and forklifts.
- Safety devices shall not be removed, except when repairing.
- All repairs of equipment shall be made at the designated repair shop.
- Dozer blades and loader buckets shall be lowered when not in use.
- There are areas of construction activity where mechanization cannot take the place of human muscle. It is in such areas that the majority of injuries occur.
- The important factor in manual handling is that a person should know his capabilities and ask for assistance when the load is beyond his capabilities.
- In dual lifting, partners should ideally be of approximately the same height and weight so that the loads do not become unevenly distributed.
- Loads, even when properly lifted, can slip and the person lifting must be prepared for such an eventuality. Safety footwear is a must to protect the feet. Gloves must be worn to protect the hands from laceration or splinters and to give added protection if the fingers are tapped between the loads and other surfaces.
9.2 LADDERS
Ladders present one of the major hazards in construction work and their use is the use of many serious accidents. Great care should be used in the selection of the proper size of the ladder for intended use.
- An analysis of accidents involving ladders reveal that the four principal causes of such accidents are: climbing or descending improperly; failure to secure the ladder top and/or bottom; structure failure of the ladder itself, and carrying objects in the hands while climbing or descending
- Job-made ladders must be constructed to conform to the established standards
- Only heavy duty grade manufactured ladders should be used on the job.
- Broken or damaged ladders must not be used. Repair or destroy them immediately.
- Do not splice short ladders together to make a longer ladder.
- Ladders should not be placed against movable objects.
- The base of the ladders must be set back to a safe distance from the vertical approximately one-fourth of the working length of the ladder
- Ladders used for access to a floor or flatform must extend 3 feet above the landing.
- The areas around the top base of the ladder must be free of tripping hazards such as loose materials and electrical cords.
- Barricades or guards must protect ladders, which project passageways, or doorways where they could be struck, moving equipment or materials being handled.
- One must face the ladder at all times ‘when ascending or descending.
- Shoes must be free of mud, grease or other substances, which could cause slip or falls.
- Always move the ladder to avoid overreaching.
- One should not carry materials up a ladder. Use a hand line.
- Nobody should be allowed to stand on the top steps of the stepladder.
- Metal ladders must not be used for electrical work or in areas where they could contact energized wiring. The use of metal ladder is restricted to special applications where the wooden ladders are not practical.
- Ladders should never be used in horizontal position as runways or scaffolds.
9.3 SCAFFOLDINGS
All scaffolding works
to be done inside the project site should
comply with Customer Scaffolding
Safety Standard.
Where work cannot be done safely on the ground or on permanent structure, scaffolds or other means of support should be provided and maintained.
9.3.1 Requirements for all Scaffoldings
- Scaffolds or temporary floor should be provided for all work that cannot be done safely from the ground or from solid construction.
- Lumber used in construction of scaffolds, or temporary platforms should be sound, of good quality and should be reasonably free of defects or any other condition which would material impair its strength for the purpose intended.
- All scaffolds or temporary flatforms constructed of materials other than wood should at least meet the requirements for wood construction in strength and rigidity.
- Scaffolds or working flatform of any nature should be securely fastened to the building or structure. If independent of the building, it should be guyed or braced to prevent it from breaking away.
- All scaffolds or other working fiatforms more than 6 ft. above adjoining surface shall be effectively guarded with a guardrail. Such guardrail should have a minimum of 40 inches high.
- Suspended scaffolds should have a guardrail, an intermediate rail and toe board.
- No scaffolds should be used for storage of materials, except as required for immediate needs.
- Every worker working on scaffolds must be provided with and required to wear Full body harness, which shall be attached to a static line independently fastened to a building. The static line should be only sufficient length to permit the work of the rigger to be performed so that, in the event of a fall, it will be as short as possible.
- Scaffolds and ladders should be inspected as required. Loose or missing parts, cracks, splinters in uprights, braces and steps be noted and repaired at once.
- Scaffolding should be constructed of sound material, securely fastened and supported. Plank for scaffolds should not be less than two inches in thickness.
- Never construct a scaffold with a span longer than eight feet between supports.
- Scaffolds should be dismantled and returned to stock when not in use. Nails should not be left in dismantled scaffolds.
- Scaffolds and ladders built by others should be carefully inspected before use.
- Scaffolds should not be overloaded beyond their working capacity.
- Only authorized scaffolders can erect, dismantle and modify scaffoldings.
- Jumping and hanging of tools on any part of the scaffolding is not allowed. Neither must heavy materials be dropped on, or anything thrown from the scaffold.
- Workers shall not work on a scaffold installed outdoors during storm nor high wind. Re-inspection of scaffolds should be done after a storm/typhoon or other calamities, which can affect the integrity of the scaffolds; utilization of such scaffolds will only be allowed after inspection.
- A safe means of access to the scaffolds should be provided. When ladder is used, it should be in good condition and its upper end securely fastened to prevent tipping.
- Good housekeeping should be observed on scaffolds at all times.
9.4 TEMPORARY ELECTRICAL INSTALLATION
This section covers accident prevention practices in temporary electrical installation. Electrical hazards differ from other hazards found in construction work because there are no advance warning for human sense. In contrast an approaching vehicle can be heard, and the prospect. of fall can be seen.
9.4.1 General Requirements
- All temporary electrical installation works must be earned out by experienced electricians and no matter what the voltage is used, should always be treated seriously.
- Before connecting temporary electrical installation to existing facilities, prior approval must be obtain from the customer's Authorities.
- Before any part of a newly installed electrical system or equipment is energized, it must be thoroughly tested.
- Care must be taken to ensure that distribution wires are subjected to rough treatment that could damage them. All wires should be double insulated.
- Temporary electrical cables must be covered or elevated so they do not create tripping hazards.
- Splices in electrical cables must retain the mechanical and dielectric strength of the cable.
- Energized junction boxes and circuit breaker panel shall be covered at all times.
- Generator sets, transformer banks and high voltage equipment shall be enclosed with fence. Warning signs of DANGER HIGH VOLTAGE shall be posted.
- A GFCI (Ground Fault Circuit Interrupter) shall be used in conjunction with the electrical power tools.
- Adequate number of circuit breakers and safety switches of adequate capacity shall be provided. Overloading beyond the noted capacity shall not be allowed.
- Multiple connections of cables from one safety switch and/or circuit breaker shall not be allowed.
- When it is necessary to work in the vicinity of live electric lines; the responsible Supervisor must consult the Customer's representative who will determine whether or not the electric lines can be energized.
9.5 PAINTS AND COATINGS
Employees engaged in surface preparation and paint application can be exposed to the dangers of fire, explosion, chemical burns, toxic fumes, dust and insufficient air. This section explains how to minimize these hazards.
- In paint, It is normally the vapor that is flammable and generally the other components are less dangerous and non-explosive.
- Explosive limit is the range of vapor concentrations that are potentially explosive. The Lower Explosive Limit (LEL) is typically a level readily obtained in the area near opened solvent containers and near the nozzle of a spray painting gun in operation.
- Flash point is the Lowest temperature at which a liquid will give off sufficient vapor to ignite when exposed to open flame.
- Fire Precautions
- Smoking or the use of open flames is not permitted within vicinity.
- All electrical lighting and equipment shall be explosion proof.
- Solvent and paints shall not be applied to surfaces warmer than ambient temperatures.
- Ventilating equipment shall be used for work in confined areas.
9.6 HEATH HAZARDS
- Toxicity - Most of the solvents contained in paints or used for cleaning are toxic in varying degrees. The dangers can arise from inhalation, ingestion, or skin absorption.
- Skin Irritations - The vapors from many solvents can cause mild and to quite severe allergic skin irritations. The alkaline catalyst in many epoxy paints can cause severe chemical burns if not washed off immediately with water.
- Strong de-greasing solvents such as ketoses aromatic hydrocarbons remove natural skin oils and promote skin cracking. Adequate readily available washing facilities should be provided on site so those workers do not have to use thinners for washing up.
- Barrier creams are substances rubbed on the skin for protection against paints and solvents.
9.7 EXCAVATION
One of the major hazards in excavation work is the presence of underground facilities, such as utility lines and sewers. If these are dug into and damage in any way, there may be injury to men, interruption of service, contamination of water, disruption of process and expensive delays.
9.7.1 Excavation Requirements
- Before any attempt is made to excavate, Excavation Permit must be approved and checked by the Engineering representative from PBR for location of underground lines and.
- Establish a proximity limit for machine operations and complete the excavation by manual digging near underground lines.
- When Manual Excavation is being done, workers must be warned about living picks, paving breakers, or other power tools through the envelope of buried facility.
- Qualified personnel should be assigned to work on open excavations adjacent to a building and lower than wall or column footings and machinery or equipment foundation. Thorough study on the amount and strength of shoring required must be done before work begins.
- Determine the need of slut piling, shoring and bracing.
- Excavated materials should be placed at least 24 inches from the edge of excavation unless toe board or other effective barricades have been installed to prevent fallback.
- When the excavation must remain open for the duration of the construction work, barricades, fences, and warning signs are necessary.
- Support system shall be planned and designed by a competent person and meet accepted engineering requirement when excavation is more than 20 ft. in depth adjacent to structure or subject to vibration.
9.8 BEFORE EXCAVATION, CHECK THE FOLLOWING:
- Soil condition
- Proximity to buildings, utilities, heavy traffic highways, and other source of vibration.
- Ground that has been previously disturbed
- Closeness to streams, old sewers, underground cable and conduits
- Equipment, personal protective equipment, shoring materials, signs, barricades, lights, machinery, etc.
9.9 DURING EXCAVATION
- Changing ground condition particularly during rainfall.
- Adequacy and condition of shoring and sloping as job progress.
- The way in and the way out of excavation.
- Changes in vehicle traffic patterns. Trucks must be kept away from trench wails.
- Positioning of heavy equipment or material.
- Proper positioning and adequacy of bracing to prevent shoring from moving.
9.10 WELDING AND CUTTING
Welding and cutting are safe operation when proper precaution are carried out. Where equipment is defective or there is no proper ventilation of work place, then hazards will arise.
9.10.1 General Requirements
- Obtain Hot Work Permit before starting welding or cutting in a restricted area.
- All equipment must be in good condition.
- Adequate fire fighting equipment shall be provided. Minimum required 20 lbs Class ABC fire extinguisher or 10 lbs of C02.
- Molten metals and sparks must not be permitted to fall on gas cylinders, flammable materials, or operating equipment.
- Drums which have contained flammable liquids must not be used to support work to be welded, burned or gas cut.
- Cables and hoses must not cause tripping hazards or be exposed to damage.
- Craftsmen must use the prescribed personal protective equipment for the job.
- Fire watchman must be assigned for every hot work be done, watchman must not leave time area where hot works are being done without replacement and proper turnover. Watchman must also wear traffic vest for proper identification.
- A stand-by fire hose must also be provided on site to assist and reduce/eliminate falling hot slugs of welding and gas cutting.
9.10.9 Maintain adequate ventilation in an enclosed space workplace.
10. FIRE PREVENTION AND PROTECTION
10.1 FIRE PREVENTION
- Before any hot work is started within a restricted area the necessary work permit must be secured.
- All restriction listed on the permit must be followed at all times by a personnel involved.
- Smoking is prohibited inside the project site.
- When fire hazards exist near welding and cutting operations, they must be covered with fire resistant materials and continually watched during the operation.
- Combustible and flammable materials must be stored away from buildings and operating equipment.
- Equipment with internal combustion engine must be refueled only when engine is stop.
- Flammable liquids must not be taken into a restricted area unless only when the engine is stop.
- Explosive liquids and gasses must not be permitted to enter the drainage system.
- Good housekeeping practices minimize the fire hazards.
11. ALERTNESS AND CONTIGENCY
Emergency Procedure
Engineer will ensure that every management staff supervisors and workman on the site fully understand the procedures, and the action to be taken during emergency situations.
Developing Emergency Procedure
The following will be considered to establish emergency procedures.
- Coordinate with the customers representative in establishing emergency procedure.
- Make a list of available emergency services and confirm their communication channels.
- Ensure that the contractors clearly understand their responsibility and role in the site emergency procedure.
- Designate first aid/medical supplies, and other material and equipment that may be required for emergency use.
- Set up emergency response team.
- Determine emergency evacuation routes for work areas and the construction site.
- Establish personnel staging area or assembly points for evacuees.
- Make sure that all personnel clearly understand emergency warning siren signals or other warning signals used by the Customer or other authorities.
- Provide summarized communication diagrams necessary maps, and display them at proper places in the site.
- Designate a supervisor to conduct a head count and give instruction to evacuees as necessary.
- Post emergency information for each work area on the site.
- Conduct emergency procedure drill periodically.
12. SITE DISCIPLINE
Personnel breaking the site safety rules and regulations, whether deliberate or not, shall be liable to disciplinary action not excluding dismissal from work.